Polypropylene (PP) is one of the most widely applied recyclable plastic materials worldwide and is already extensively used in healthcare applications.
In medical technology, the rapidly emerging field of additive manufacturing provides manifold opportunities for patient specific solutions. So far, most of the materials cur- rently used in 3D printing do not meet the medical and techni- cal requirements. Substantial progress has been recently made with polypropylene (PP) in extrusion based 3D printing. As specialist for 3D printing with polypropylene the PPprint GmbH has established itself on the market. The company pro- vides innovative products that make 3D printing with PP straightforward. PPprint’s latest innovation is the recently launched world’s first breakaway support material which ena- bles 3D printing of even more complex PP-structures with overhangs and openings.
In the area of medical technology additive manufacturing offers new possibilities to produce patient specific individualized products and opens up various and yet unexplored areas of application. This is of particular interest for developers, desig- ners, and producers of medical devices. However, developers often face the problem that 3D printing can be used to create interesting geometries, but the resulting 3D printed objects often do not meet the product quality required for the desired application. The main reason for this is the unsuitable choice of a material with adequate performance for the selected 3D manufacturing process.
Medical technology demands materials that fulfill numerous chemical, biological, and technical requirements. Depending on the application, break-resistant and flexible, but at the sa- me time easy-to-clean and sterilizable products are needed. In order to establish 3D printing in the medical industry, suita- ble materials must be developed that meet the medical-speci- fic requirement profile. The selection of a suitable material for a specific application is closely linked to the applied manufac- turing process. The most common currently applied additive manufacturing processes are 3D printing with reactive liquid materials, 3D printing with powders, and extrusion-based 3D printing with melted thermoplastics.
In recent years, extrusion-based 3D printing has esta- blished itself as the dominant force in the market and the num- ber and quality of 3D printers available is constantly evolving. The key advantages of extrusion- based 3D printing are cost savings in terms of investment, material, maintenance and production costs. However, the common de- veloped materials for extrusion- based 3D printing, such as PLA and ABS, do not provide the requi- red performance profile for appli- cations in medical technology. Here, the recent developments of the material polypropylene speci- fically for extrusion-based 3D printing make an important step towards a solution.
Polypropylene the material of choice
When searching for a suitable material in medical technology, the number of materials that are certified for use in medical devices is rapidly becoming limited. Among the certified materials is polypropylene (PP). Well-known from injection molding and extrusion, this material is one of the most widely used plastics worldwide and has proven its broad applicability in numerous technical and medical applications over the past decades. From a sustainability point of view, PP is a plastic that can be easily and efficiently recycled and does not contain plasticizers. PP also has excellent resistance to chemicals such as acids, bases, alcohols, and water. Most important for applications in the field of medical technology is that PP grades are skin-friendly and classified as not harmful to health. Another decisive factor for the use of PP products is the possibility of sterilization and easy cleaning for example in a dishwasher. Unlike other common materials used for extrusion-based 3D printing, polypropylene combines the above properties in an excellent manner.
For applications as orthoses or orthopedic aids, the combination of break resistance, semi-flexibility, and low density of PP offers patients a high level of comfort and enables lightweight 3D printed products which can easily withstand mechanical stress. In this context, extrusion-based 3D printing of PP allows the realization of novel and complex geometries that optimally support the stabilization, immobilization, relief, guidance, or correction of limbs or the trunk. Consequently, these individually manufactured products increase wearing comfort and improve the healing processes. A se- lection of extrusion-based 3D printed orthoses and orthopedic aids made from PP by the PPprint GmbH is shown in Figure 1.
In other areas of medical technology, 3D printing with PP offers ap- plications for many medical products tailored to the needs of the patient. These include for instance shoe insoles that are already produced using additive manufacturing processes. The sole of the foot is scanned and, based on this data set, a perfectly fitting shoe insole is 3D printed. In addition, there are numerous application possibilities for individualized adaptation, standing or sitting assistance devices, up to fixtures for communication aids. For all these applications, the applied material is of crucial importance.
Extrusion-based 3D printing of polypropylene
For a successful extrusion-based 3D printing of PP, three critical components are necessary (Figure 2). First the printed material it- self should have low warpage and high interlayer bonding strength. Secondly, the 3D printing build surface has to allow a reliable 3D printing of PP parts and a non-destructive and residual-free re- moval of the finished part. Third, a support material is required to print complex structures with overhangs and openings. The PPprint GmbH solved these three challenges.
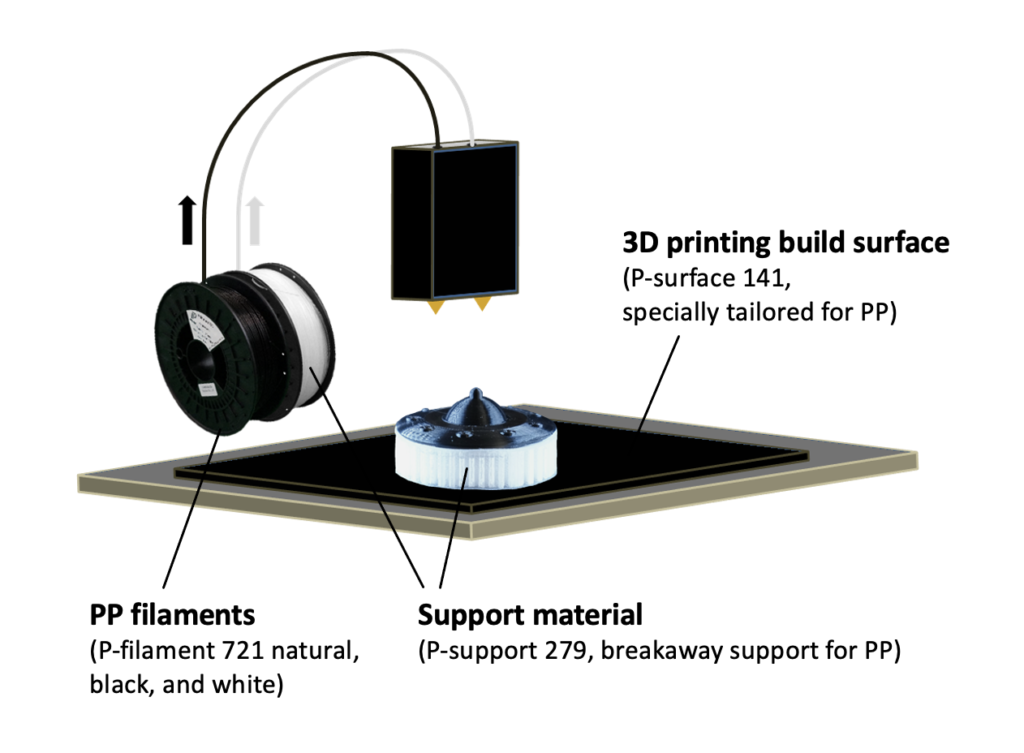
PPprint is a start-up originated from the University of Bayreuth and can build on decades of research experience of its founders in the field of polyolefins. The product portfolio includes the PP filament “P-filament 721“ which is available in the diameters of 1.75 mm and 2.85 mm and in the colors natural, black, and white. The filaments offer low warpage and very high interlayer bonding strength. In addition, 3D printed parts of “P-fialment 721 natural“ are certificated for biological safety according DIN EN ISO 10993-5, which is important for medical products in contact with skin. In addition, PPprint develoved a special 3D printing build surface “P-surface 141“ which enables reliable and reproducible printing of PP. The 3D printed parts can be easily and defect-free removed from the “P-surface 141“ at elevated temperatures. The latest development of the company is the breakaway support filament “P-support 279“ specially tailored for PP. This support material adheres very well to PP printed parts and can be easily and cleanly removed at elevated tempe- ratures. With this portfolio, PPprint combines all necessary components under one roof to successfully print complex 3D printed parts made of PP. PPprint GmbH also offers strong customer support and a printing service for PP parts in its own 3D printer factory.
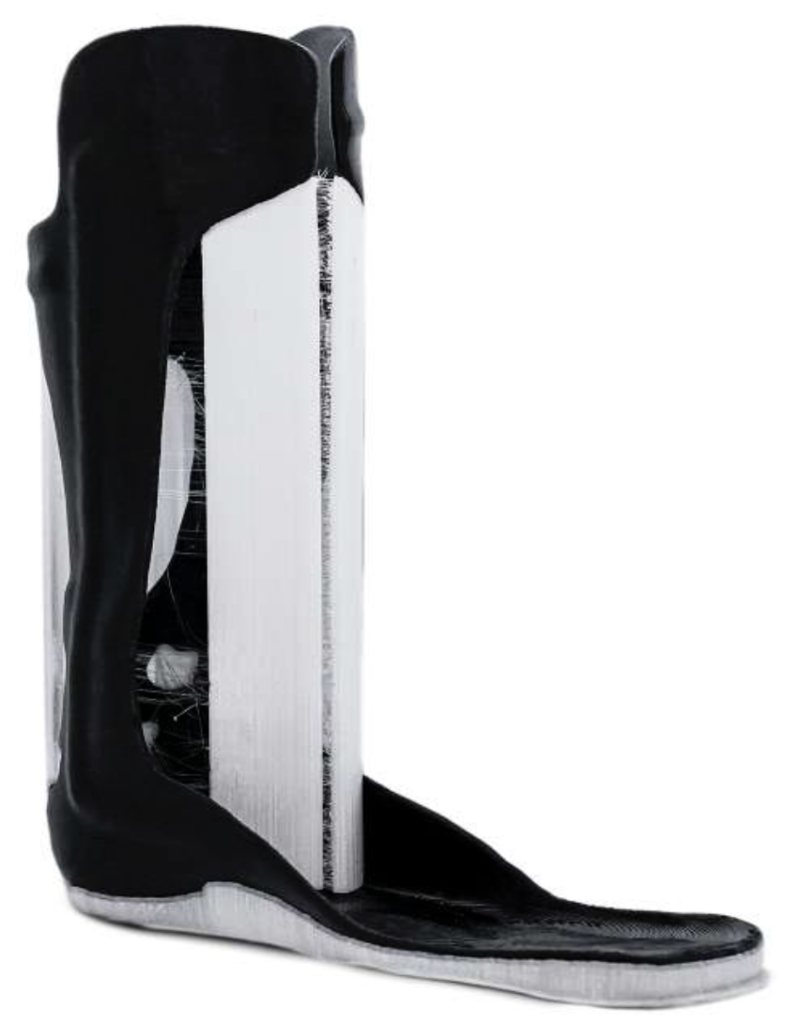
A new support material tailored for PP allows 3D printing of more complex geometries
With „P-support 279“, PPprint GmbH offers the world’s first breakaway support material especially developed for polypropylene, which allows the realization of even more detailed and complex structures containing bridging, overhangs, and openings. An illustrative example of a 3D printed leg splint (black) made from PP with support ma- terial (white) is shown in Figure 3. The support material has high stiffness, low warpage, and excellent adherence to the printed PP part and the “P-surface 141“. In addi- tion, it can be advantageously used to print rafts and sup- port structures on top of PP. The support material can be cleanly and easily removed after a short heating. Further- more, a breakaway support has the particular advantage that no solvent or aqueous polymer containing waste is ac- cumulated. In addition, the thermoplastic breakaway sup- port material “P-support 279“ can be recycled easily, which benefits sustainability.
Author:
Sebastian Schmidt
Co-Founder and Product manager PPprint GmbH
The article was published in the international edition for 2021 of MEDengineering and can be found at the following link:
https://med-eng.de/wp-content/uploads/sites/10/2021/01/medeng_international_online.pdf?fbclid=IwAR1sXKa7XrLuEqTwogMBEjRi1WjbabxHGrEDU_Dx9CQoDEOq54pCogNOhIs#page=12
More information on the advantages of PP can be found at: https://www.ppprint.de/#vorteilepp